How to improve the process
2023-08-18
1. Methods for improving surface finish
It is mainly divided into two types: adding corresponding processes and improving and adding corresponding processes on the original process: adding polishing, grinding, scraping, rolling and other processes can not only improve the smoothness but also improve the accuracy; In addition, ultrasonic rolling technology, combined with metal plastic fluidity, is available both domestically and internationally, which is different from traditional cold work hardening by rolling. It can improve roughness by 2-3 levels and also improve the overall performance of materials.
2.How to improve the process
① Reasonably select cutting speed. Cutting speed V is an important factor affecting surface roughness. When processing plastic materials, such as medium and low carbon steel, lower cutting speeds are prone to the formation of scales and burrs, while medium speeds are prone to the formation of chip deposits, which will increase the roughness. Avoiding this speed range will reduce the surface roughness value. So continuously creating conditions to improve cutting speed has always been an important direction for improving the level of technology.
② Reasonably select the feed rate. The size of the feed rate directly affects the surface roughness of the workpiece. In general, the smaller the feed rate, the smaller the surface roughness, and the smoother the workpiece surface.
③ Reasonably select the geometric parameters of the cutting tool. Front and rear corners. Increasing the front angle can reduce the deformation and friction of the material during cutting, and also reduce the total cutting resistance, which is beneficial for chip removal. When the current angle is fixed, the larger the back angle, the smaller the blunt radius of the cutting edge, and the sharper the blade; In addition, it can also reduce the friction and extrusion between the rear cutting surface and the machined surface and transition surface, which is beneficial for reducing the surface roughness value. Increasing the arc radius r of the tool tip can reduce its surface roughness value; Reducing the secondary deflection angle Kr of the tool can also reduce its surface roughness value.
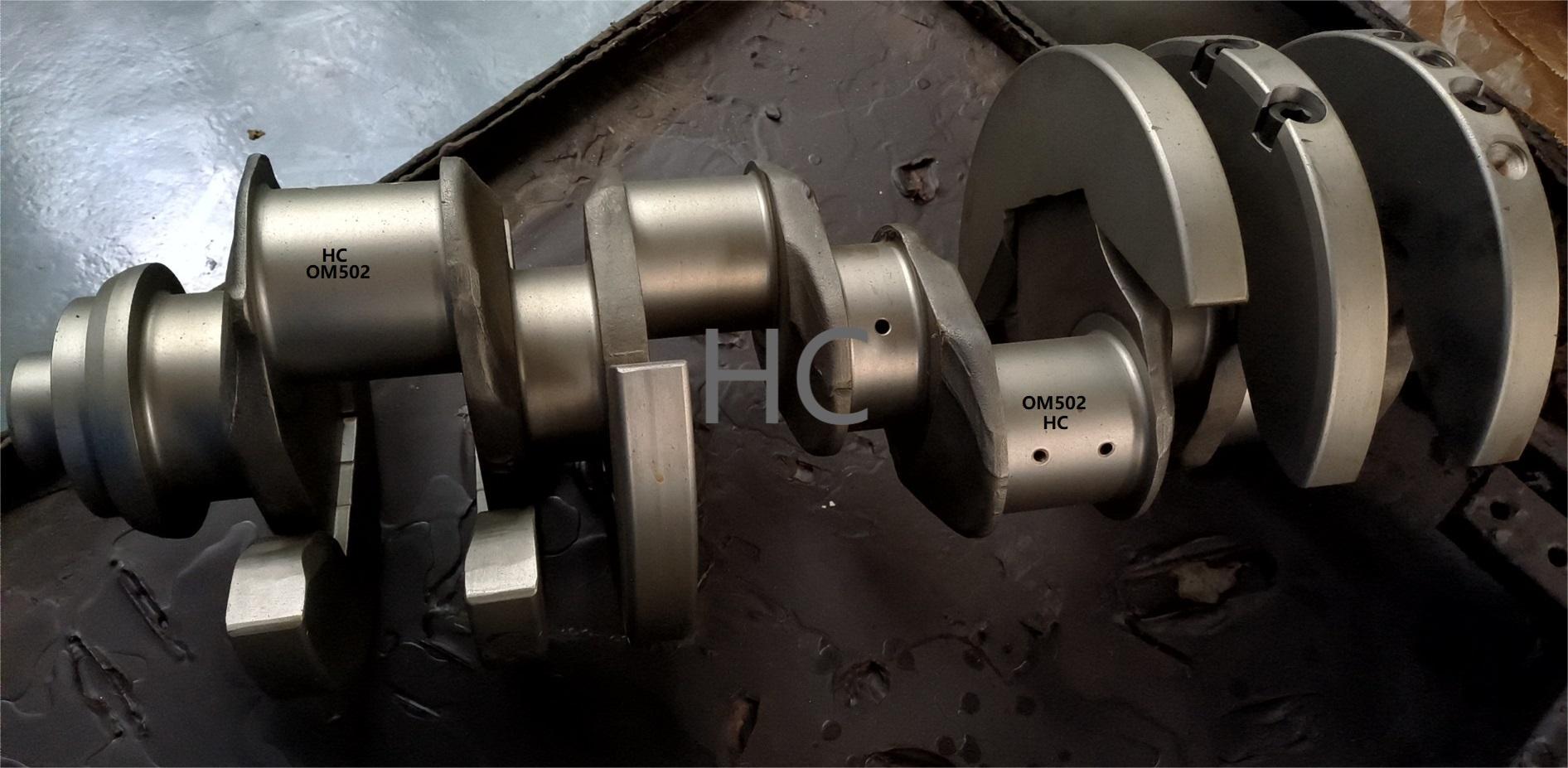
④ Choose the appropriate tool material. Tools with good thermal conductivity should be selected to timely transmit cutting heat and reduce plastic deformation in the cutting area. In addition, the cutting tool should have good chemical properties to prevent affinity between the cutting tool and the processed material. When the affinity is too high, it is easy to produce chips and scales, resulting in excessive surface roughness. If hard alloy or ceramic materials are coated on its surface, an oxidation protective film is formed on the cutting surface during cutting, which can reduce the friction coefficient between it and the machined surface, thus improving the surface smoothness.
⑤ Improve the performance of the workpiece material. The toughness of a material determines its plasticity, and with good toughness, the possibility of plastic deformation is greater. During mechanical processing, the surface roughness of the part increases.
⑥ Choose the appropriate cutting fluid. The correct selection of cutting fluid can significantly reduce surface roughness. Cutting fluid has cooling, lubrication, chip removal, and cleaning functions. It can reduce the friction between the workpiece, tool, and chip, carry away a large amount of cutting heat, reduce the temperature of the cutting zone, and timely remove small chips.